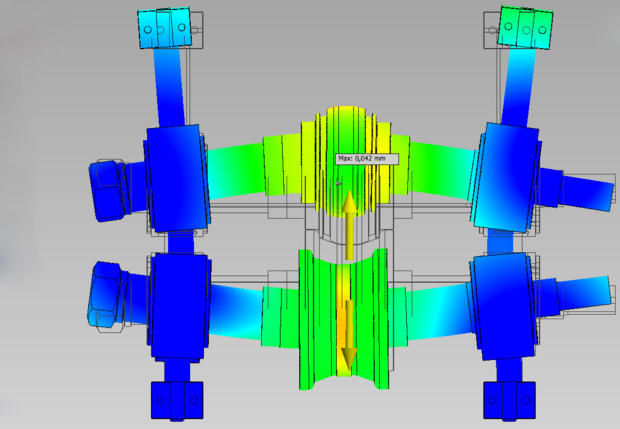
The virtual rollforming line
Using simulations based on finite elements it is possible to avoid not only costly defects and insufficient product quality. Intelligent collaboration with further COPRA software solutions allows simulation results to be immediately available for optimization and error correction in COPRA RF. If required, the flower pattern can be adjusted automatically. As a side effect, consistent simulation of the forming strategy generates valuable know how within the company.
Material alterations during the rollforming process are often problematic for manufacturers ofprofiles and tubes, but do not pose a problem for COPRA FEA RF. Common defects likecorrugation of sheet edges, twists or other bends can often be avoided beforehand through verification.
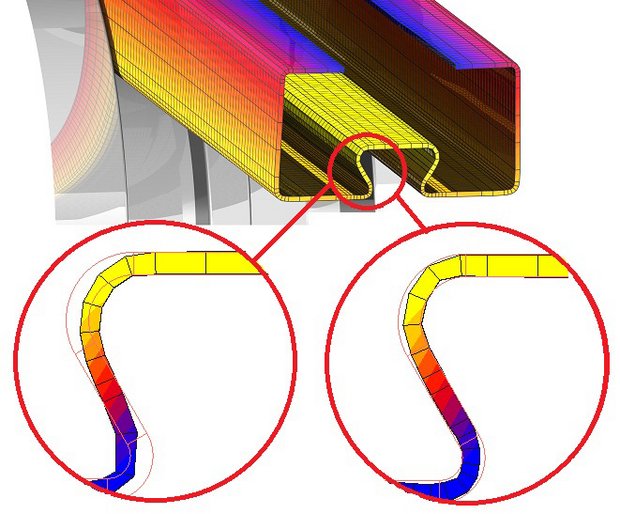
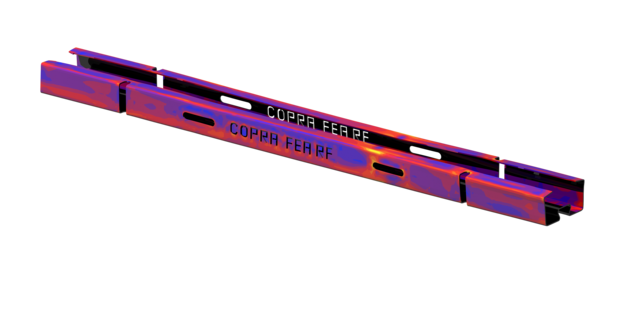
Process optimization using simulation
The quick and reliable simulation with COPRA FEA RF not only optimizes the rollforming process, but also reduces wearout of roll tools to a minimum. Using finite element simulations, the greater part of the implementation of a rollforming line can literally be conducted by the software. Consistent simulation also avoids machine downtimes and ensures a cost-effective process.
Keep track of everything in complex forming processes: At the end of a simulation, COPRA FEA RF generates a dynamicanimation of the rollforming process and visually displays the results. This includes such crucial information like forming forces, driving torques as well as pressure and tension conditions. The data of the simulated cross sections will be automatically compared to the data derived from the design. Acomprehensive, three dimensional representation of the (virtual) product is also generated.
- Automatic and extremely fast generation of FE-model
- No FEA specialist required - every designer experienced in rollforming can work with COPRA FEA RF
- Easy and fast optimization of roll sets
- Virtual implementation and simulation of roll designs
- Advanced Restart - Adaption of the computational mesh during design
- Stand rigidity: Changes of the rollforming gap due to the forming forces calculated reliably
- Calculation of necessary driving moment
- Dynamic animation of forming process
- Derives the rotational velocity of passive axes
- Visualization of forming forces, detailed for all axes
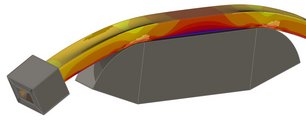
Process simulation not only reduces expences for prototypes, roll tools and the commissioning of rollforming lines. Consistend and documented verification of design also generates valuable know how within the company.Quite a number of customers report medium-term cost reductions due to a more efficient rollforming process and reduced wearout of their roll tools.
Process simulation and full integration in the COPRA workflow enables profile and tube manufacturers to
- better calculate their costs
- more efficiently use their existing tools
- optimize their production process without costly trial and error cycles (incl. pre- and post-processing manufacturing steps)
- evaluate the feasibility of projects before they start
- generate know how for future projects
Automatic Report Generator
COPRA FEA RF processes the results of the simulation geared to the respective target group, enabling the project manager to keep track or the designer to select detailed result quantities due to the reproducible templates. There is even a tailored report for the operator.